Durable, Front Surface Hard Optical Coatings For Replacing Laminated Soft Coatings
Alluxa’s proprietary high speed plasma deposition technology for the first time delivers the optical performance and durability of hard coated optical filters at laminated soft coating pricing.
Soft coatings, also known as laminated coatings are well known to possess poor environmental durability, poor temperature stability, low transmission, high optical scatter and low blocking levels, yet they are still widely used due to their low cost, ready availability and legacy status. Alluxa’s proprietary high speed plasma deposition technology for the first time delivers the optical performance and durability of hard coated thin film optical filters at laminated soft coating pricing.
Soft Coating Background
Soft coatings are multilayer thin film structures composed of thin layers of ZnS and Cryolyte. They may also contain very thin silver layers. A typical soft coating is a simple band-pass structure on one substrate surface and a blocker on another as shown in Figure 1 below. The blocker may use thin layers of silver and/or they may contain an auxiliary blocking color glass or an organically died epoxy. All components are laminated together in a vertical stack in an attempt to provide some degree of environmental protection.
Individual parts are diced or cored from a larger wafer. As the coatings are fragile and moisture sensitive, the edges of the coated substrate may be scribed away with the goal of lengthening the amount of time before noticeable and unsightly environmental degradation occurs. All soft filters fail over time, where the lifetime is a function of the environment and the care in construction of the filter. One to five years is a typical expected lifetime in normal office type environments.
The low cost of soft coatings is derived from a combination of the low capital cost of the deposition equipment, rapid cycle times and simple and inexpensive float glass substrates. As the load sizes are relatively low, and they contain significant handling costs due to the sealing and ring assemblies, the cost vs. volume curve asymptotically flattens after only a few dozen 1 inch parts, or a handful of 2 inch or larger parts.
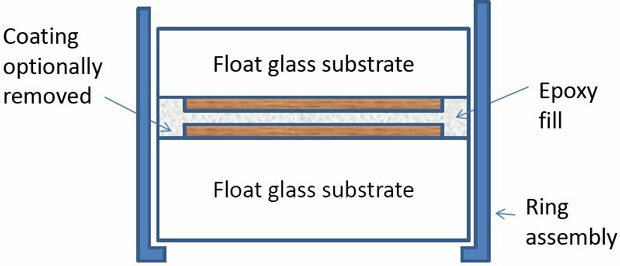
Figure 1. A typical soft coating has three structures laminated together to help provide moisture resistance. The structure is typically 2-5mm in thickness and mounted in a ring to further try to restrict humidity ingress.
Soft coatings have large optical losses from both scatter and absorption in the visible and near infra-red, which further increases in the UV and blue. Figure 2 shows the spectral function of a series of typical commercially available dielectric (no silver) laminated soft coatings across the visible band. Soft coatings typically also have severe ripple in the pass-band which not only lowers average transmission, but also adds a degree of uncertainty to the instruments spectral function. The ripple and uncertainty of the spectral functions of soft coatings are a result of the manual and labor intensive nature of the deposition, which provides a much greater degree of variation to performance as compared to computer controlled hard coatings.
Figure 2. Soft coating designed for high transmission that contains no silver layers. The transmission can rise above 80% in the green/red, but drops to less than 50% in the UV blue. Also note the severe ripple in the pass-band attributable to the lack of computer controlled deposition control.
Alluxa Plasma Deposition of Hard Coatings
Hard dielectric films produced by Alluxa’s advanced high speed plasma deposition process are nearly lossless, with extinction coefficients in the low ppm range from the UV to the IR. They are made using sophisticated computer control algorithms that control thickness of each layer to an atomic monolayer or less, and consequentially they have much higher transmission and dramatically flatter pass-bands. Figure 3 shows comparable fully blocked filters built using Alluxa’s hard coatings that are designed as drop in replacements of the soft coating filters shown in Figure 2.
Figure 3. Hard coatings by Alluxa on a single side of a glass substrate. Note that with an AR on the back the transmission would approach 100%. Also note the inherent improved “squareness” of spectral shape, which helps S/N by increasing transmission as well as blocking. Improved shape is direct result of the repeatability of automation.
Improved Temperature Stability
Depending on substrate selection, Alluxa hard coatings have a temperature stability of less than 5 part per million (ppm) of wavelength. Soft coatings have a typical value of 50 ppm, which means for the instrument design the filter must be controlled to +/- 15C for a 1nm filter tolerance. For telecom applications, Alluxa routinely builds filters to less than 1 picometer per degree Celsius at 1550m, well less than 1 part per million change in wavelength.
Transmitted Wavefront Error (TWE)
Alluxa can provide filters with TWE values of less than ¼ wave peak to valley as shown in Figure 4 if the user requires. For most designs, the TWE of the finished filter is essentially identical to that of the uncoated substrate. Soft coatings with their laminated structure would have to undergo a complicated post lamination grinding and polishing step to approach a single wave per inch of TWE.
Figure 4. Transmitted wave front error of fully blocked band-pass Alluxa hard coating on fused silica substrate. The substrate is 2 inches in diameter.
Ultra-Narrow Filters
Because of the excellent stability of Alluxa hard coatings , extraordinarily narrow films can be built and used in instruments without temperature control. Figure 5 shows a multi-cavity filter of less than 0.4nm at 1550nm. Figure 6 shows a typical laser filter in the visible.
Figure 5. Ultra-narrow band filter built using Alluxa’s plasma deposition technology. The bandwidth is approximately 0.3 nm in bandwidth at 1570nm.
Figure 6. Consecutive runs of an ultra-narrow band filter at 632.8nm built using Alluxa’s plasma deposition technology. The bandwidth is approx. 2nm wide.
Cost Comparisons
While soft coatings are manufactured in inherently lower cost bell jar evaporation chambers, they also have much smaller batch sizes and are almost exclusively manual in operation, which adds cost and variability while decreasing yield. Alluxa processes are fully automated ensuring repeatability, continuous operation, and low direct labor cost.
For OEM applications, Alluxa’s hard coatings have much larger load sizes than typical soft coatings. As volumes approach 20-30 one inch parts, Alluxa is capable of matching or beating the cost structure of soft coatings, while providing the reliability and performance advantages of hard coating technology.
Table 1
Cost comparison of Alluxa hard coatings against soft coatings.
Parameter | Soft Coat | Alluxa Hard Coat | Notes |
---|---|---|---|
Labor Content | Fully Manual, No Automation | Minimal Labor, Full Automation | Soft coat requires skilled operators |
Load Size | Moderate | Medium to Large | Hard coat can have bigger load sizes |
Cycle Time | Fast | Moderate | Alluxa has the fastest hard coating cycle time in the undustry |
Repeatability | Poor – Moderate | Excellent | Full automation guarantees repeatable results |
Capital Equipment Cost | Low | Moderate | Alluxa builds its own coating machines to provide lower capital cost |
Summary
Soft coatings possess poor environmental durability, poor temperature stability and low transmission, high optical scatter, yet they are still used mostly due to low cost. Alluxa’s advanced high speed deposition technology has finally enabled hard coatings to compete on price with soft coatings, even in small batch sizes. Alluxa’s filters offer dramatically improved transmission, spectral shape, and lifetime.
Alluxa
Alluxa designs and manufactures next generation hard coated optical filters using a proprietary plasma deposition process in Santa Rosa, CA. Alluxa’s unique, purpose-built deposition platform and control systems were designed, developed, and built by our team in Santa Rosa, CA to address the demanding requirements of the next generation of systems and instruments. This unique technology allows Alluxa to create the world’s most challenging filters at breakthrough price points.
Contact Alluxa for more information at info@alluxa.com
or visit our website at https://alluxa.com
All content copyright ©2012 Alluxa